Comprehensive Review of Foam Concrete: Materials, Properties, Microstructure, and Applications
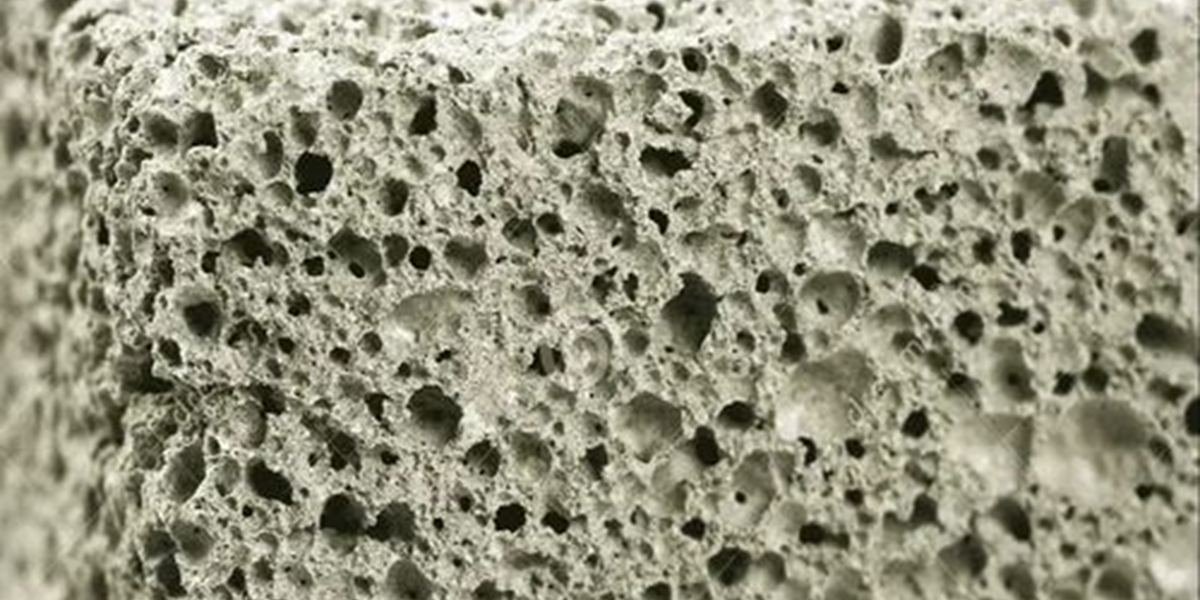
Foam concrete is a lightweight cementitious material created by mixing air voids into the cement matrix using foaming agents. The resulting material is characterized by low weight, minimal aggregate use (excluding coarse aggregates), and high flowability. With densities ranging from 400 to 1600 kg/m³, foam concrete can be up to 80% lighter than conventional concrete. Its compressive strength varies from 0.2 to 10 MPa depending on its composition and application. Known for its thermal insulation, acoustic dampening, and fire resistance, foam concrete is widely used in structural, partitioning, and insulation applications, as well as in void filling and trench fill projects.
Historical Development
Foam concrete was first used in the 1920s as an insulating material. Over time, particularly during the 1930s and 1940s in the Soviet Union, foam concrete saw expanded applications in wall panels and floorboards. In the 1950s, protein-based foaming agents were introduced, leading to advancements in stabilization and large-scale production. By the 1970s, foam concrete found applications in oil well cementing and excavation projects. Today, it is extensively used in countries such as Turkey, Germany, and China for both residential and commercial purposes.
Production Methods
There are two primary production methods for foam concrete:
- Inline Method: A combination of cement, sand, and foam is blended to achieve the desired consistency. This method can be subdivided into:
- Wet Inline System: Here, wet materials are blended with foam using static mixers, enabling continuous density monitoring.
- Dry Inline System: Dry materials are measured and mixed with foam at a later stage, providing better control over density.
- Pre-Foam Method: Pre-formed foam is injected into the cementitious mix at the construction site. This method is suitable for small-scale projects like trench fill works, with density variations between 300 and 1200 kg/m³.
Composition of Foam Concrete
Foam concrete’s composition is determined by its target density. Low-density foam concrete (under 600 kg/m³) typically comprises cement, water, foam, and lightweight fillers like fly ash or limestone dust. In contrast, high-density foam concrete incorporates sand to achieve greater strength, with cement-to-filler ratios between 1:1 and 1:3.
Materials Used in Foam Concrete
- Cement: Ordinary Portland Cement (OPC) is the most commonly used binder, but magnesium phosphate cement (MPC) or sulfoaluminate cement (SAC) may be employed for specific applications requiring rapid setting or fire resistance.
- Aggregates: Fine aggregates (up to 5 mm in size) are used, as coarse aggregates can destabilize the foam structure. Recycled materials, such as glass powder or waste marble dust, are increasingly used as sustainable replacements for sand.
- Foaming Agents: Protein-based and synthetic surfactants are commonly employed. Protein-based agents create stronger, more durable foam bubbles, while synthetic agents are cheaper and easier to handle. Research by Ma and Chen (2021) indicates that synthetic foam produces more stable mixes with smaller pore sizes, leading to improved compressive strength.
- Fibers: Natural and synthetic fibers (e.g., polypropylene, glass) can be added to enhance mechanical properties like tensile strength and crack resistance. The addition of 1% polyvinyl alcohol (PVA) fibers increased the compressive strength by up to 76% in specific tests.
Microstructure of Foam Concrete
The microstructure of foam concrete consists of evenly distributed air voids ranging from 0.1 mm to 1 mm in size. These voids are created by the foaming agent and are stabilized within the cement matrix during the mixing process. The porosity of foam concrete has a significant impact on its mechanical, thermal, and acoustic properties. Smaller, well-distributed pores increase strength and improve resistance to external forces. A denser, more closed-pore structure is ideal for load-bearing applications, while open-pore structures are preferred for insulation purposes. Scanning Electron Microscope (SEM) images of foam concrete reveal that the formation of a uniform pore network contributes to its overall durability and performance under thermal stress.
Acoustic and Thermal Conductivity
Foam concrete exhibits excellent acoustic properties, making it ideal for soundproofing applications in residential and commercial buildings. Its ability to absorb and dampen sound is largely dependent on its density and pore structure. Lower-density foam concrete (below 600 kg/m³) has better acoustic absorption properties due to its higher air content and interconnected pore structure, which dissipates sound energy effectively.
Thermal conductivity in foam concrete ranges from 0.1 to 0.7 W/mK, depending on the density. Foam concrete with a density of 400 kg/m³ can achieve thermal conductivity as low as 0.1 W/mK, making it a highly effective thermal insulator. As density increases, the thermal conductivity rises due to the reduced air content and increased solid material. Foam concrete’s ability to reduce heat transfer makes it ideal for insulation in walls, roofs, and floors, providing energy efficiency in buildings.
Fresh Properties
Fresh foam concrete displays high workability, with slump values typically ranging from 150 mm to full collapse. It is highly fluid, making it easy to place in complex forms without requiring compaction. However, care must be taken when pumping foam concrete to avoid bubble collapse, which can affect its performance.
Hardened Properties
Once hardened, foam concrete exhibits compressive strength values ranging from 0.2 to 10 MPa, with the strength increasing as the density increases. The material's drying shrinkage is typically low, ranging from 0.1% to 0.35%. Its porous structure makes it highly resistant to freeze-thaw cycles, and it can operate in temperatures between -18°C and +25°C without significant damage. The material’s durability in such environments is a key factor in its growing use in cold climates and areas prone to freezing conditions.
Advantages of Foam Concrete
- Lightweight: Foam concrete significantly reduces the overall weight of structures, making it ideal for high-rise buildings and retrofits.
- Insulation: With thermal conductivity as low as 0.1 W/mK, foam concrete provides excellent thermal insulation, reducing energy costs in buildings.
- Workability: Its high flowability allows it to be easily placed in molds and hard-to-reach areas without compaction.
- Durability: Foam concrete demonstrates excellent resistance to fire, freezing, and thawing, making it a robust material for diverse environmental conditions.
Disadvantages of Foam Concrete
- Moisture Sensitivity: Foam concrete is highly sensitive to water content during mixing, which can affect strength and stability.
- Surface Finishing: Achieving a smooth finish with foam concrete is challenging due to its fluidity.
- Longer Mixing Times: Compared to traditional concrete, foam concrete requires longer mixing times, particularly for high-density applications.
Mechanical Properties and Strength Models
Foam concrete’s compressive strength is directly related to its density, with higher-density foam concrete achieving strengths of up to 10 MPa. Supplementary cementitious materials such as fly ash and silica fume improve strength and durability. Various models, such as Balshin's equation and the Power's gel–space ratio concept, are used to predict foam concrete’s mechanical performance based on its porosity and mix design.
Durability
Foam concrete is highly durable, particularly in freeze-thaw environments. In tests, foam concrete with a density of over 1000 kg/m³ has shown excellent resistance to freeze-thaw cycles. Under elevated temperatures, foam concrete maintains its strength up to 400°C before gradually losing compressive strength due to water evaporation and thermal shrinkage, making it suitable for fire-resistant applications.
Conclusion
Foam concrete is a versatile, lightweight material offering significant advantages in terms of thermal insulation, acoustic properties, and durability. Its production is straightforward, though care must be taken to manage water content and ensure proper mixing. While foam concrete’s compressive strength is lower than traditional concrete, its benefits in terms of reduced weight, fire resistance, and sound absorption make it a preferred choice for many modern construction projects. Further research into improving its mechanical properties, optimizing its microstructure, and enhancing its environmental resistance will broaden its applicability in the future.
Cellular Lightweight Concrete Technology
We are one of the leading manufacturers of CLC foam concrete equipments, and have exported to many countries around the world. We can supply machines as part of a production line, or complete turn-key manufacturing plants.
Lightweight Concrete Equipments
Share your project details with us, and we'll ensure the right team member gets back to you promptly.