Optimizing Foam Concrete for Natural Gas Pipeline Tunnel Filling
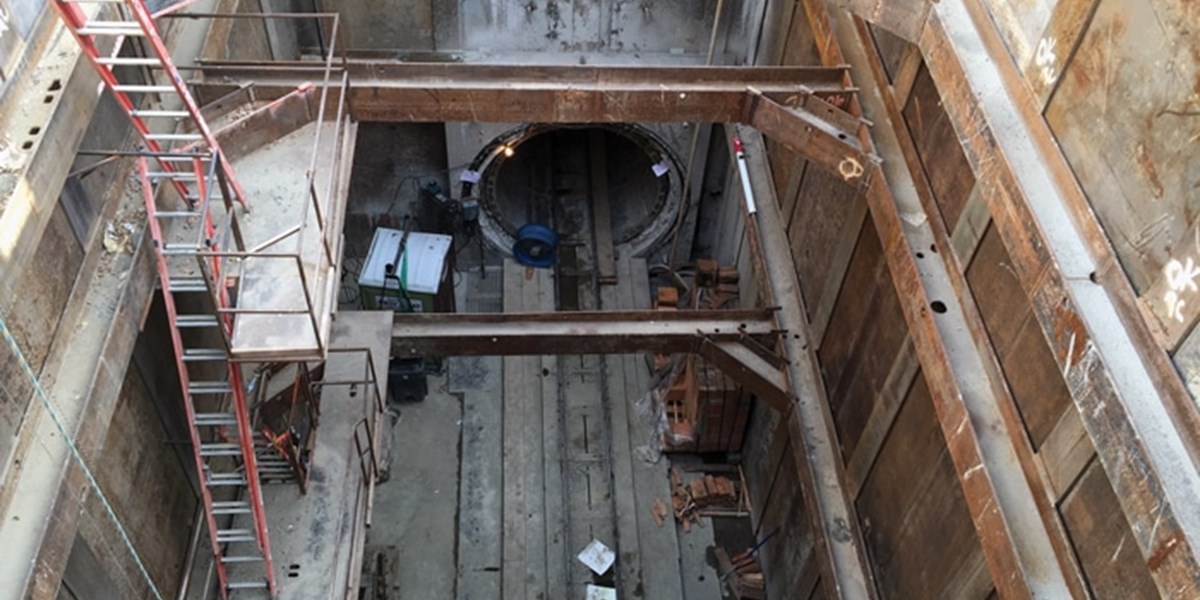
Research on the Improving Performance of Foam Concrete Applied to the Filling of Natural Gas Pipeline Cross-River Tunnel
The research conducted by Xiaosong Ma, Chunbao Li, Haiyang Chen, Yongqi Wei, Yongmei Weng, Shen Li, and Dalerjon Hojiboev focuses on enhancing the performance of foam concrete used in filling natural gas pipeline tunnels, particularly those crossing rivers. The study highlights the challenges and solutions in optimizing foam concrete to meet the specific requirements of tunnel filling, ensuring safe and efficient operation.
Introduction
Natural gas pipelines often traverse complex terrains, necessitating robust and efficient tunnel filling materials to ensure safety and maintenance. Foam concrete is proposed as a viable solution due to its lightweight, insulating properties. However, achieving the necessary balance between high density and low compressive strength has been challenging.
Research Approach
The researchers employed a synergistic optimization strategy combining orthogonal tests, univariate control, and comprehensive balance methods. Key modifications included adjusting the cementitious matrix by incorporating fly ash and polyvinyl alcohol (PVA) fibers. The optimal mix ratios were determined based on compressive strength, stability, and dry density.
Key Findings
- Compressive Strength and Density: The optimized foam concrete achieved a compressive strength of 4.29 MPa and a dry density of 1060.59 kg/m³. This balance meets the pressure requirements and anti-floating demands of natural gas pipelines.
- Orthogonal Test Results: The water-cement ratio was found to be the most significant factor affecting compressive strength and stability, followed by the addition of superplasticizer, foaming agent dilution ratio, and fly ash content.
- Water-Cement Ratio: Increasing the water-cement ratio from 0.3 to 0.6 resulted in a significant increase in compressive strength, peaking at 6.09 MPa.
- Fly Ash Addition: Fly ash addition of 25% was found optimal, improving the pore structure and compressive strength without compromising stability.
- PVA Fibers: The inclusion of 0.15% PVA fibers enhanced the crack resistance of the foam concrete, reducing surface cracking and improving overall durability.
Practical Applications
The optimized foam concrete was applied to the Yangtze River shield crossing project of the Sino-Russian Eastern Gas Pipeline. The study’s findings provide a robust framework for using foam concrete in similar large-scale infrastructure projects.
Case Study Data:
- Project: Yangtze River shield crossing project of the Sino-Russian Eastern Gas Pipeline
- Optimized Mix: Water-cement ratio of 0.35, 25% fly ash, 40 times dilution of foaming agent, 0.1% superplasticizer, and 0.15% PVA fiber.
- Performance Metrics: Compressive strength of 4.29 MPa, dry density of 1060.59 kg/m³, maximum deformation of foam concrete under operating pressure 1.61 mm, and maximum stress 3.5 MPa.
ANSYS Simulation
Simulations using ANSYS software demonstrated that the optimized foam concrete could effectively handle the stress and deformation under the operating pressures of natural gas pipelines, confirming its reliability and safety. The maximum deformation was 1.61 mm, and the maximum stress did not exceed 3.5 MPa, ensuring no plastic damage during operation.
Sustainability Considerations
The study also emphasizes the sustainability of foam concrete. By incorporating fly ash, a by-product of coal combustion, the environmental impact is reduced. Additionally, the energy efficiency and long-term durability of foam concrete contribute to lower carbon footprints for construction projects.
Sustainability Data:
- Fly Ash Addition: 25% fly ash reduces the need for virgin cement, lowering carbon emissions.
- Energy Efficiency: Improved thermal insulation properties lead to energy savings in heating and cooling, contributing to overall sustainability.
Conclusion
The research successfully optimized foam concrete for use in natural gas pipeline tunnels, ensuring enhanced performance and safety. The innovative mix design and thorough testing provide a valuable reference for future projects involving tunnel filling materials. This work underscores the potential of foam concrete as a sustainable and efficient solution in modern construction.
Cellular Lightweight Concrete Technology
We are one of the leading manufacturers of CLC foam concrete equipments, and have exported to many countries around the world. We can supply machines as part of a production line, or complete turn-key manufacturing plants.
Lightweight Concrete Equipments
Share your project details with us, and we'll ensure the right team member gets back to you promptly.