We are one of the leading manufacturers of CLC foam concrete equipments, and have exported to many countries around the world. We can supply machines as part of a production line, or complete turn-key manufacturing plants.
SMALL CLC BLOCKS PLANT WITH CAPACITY OF 10-20M3/DAY
CLC brick manufacturing plant (CLC plant) was designed and installed by THT International with the capacity from 10 to 20m3/day. This CLC block plant is suitable for the small manufacturing facility, rural or urban manufacturing facility, or for a construction company serving small areas.
This small and compact CLC plant is designed for the production of CLC blocks from the following materials: cement/ fly ash, sand, water, and foam. The producer may add the concrete additive.
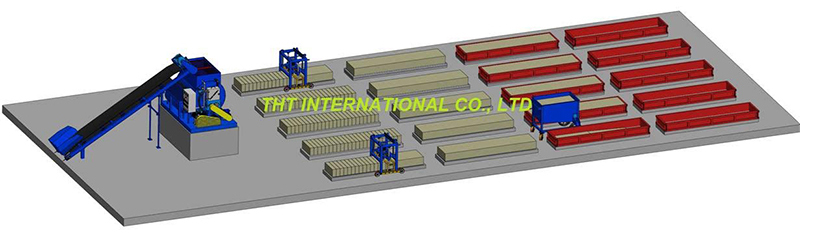
Layout design of samll CLC Block plant with MasterMix mixer and MiniCutter cutter
Advantages of small CLC plant:
- No need for large space, saving investment costs, high efficiency
- Compact design, easy to operate and maintain, good energy consumption, environmental protection.
- Modular design, high mobility, easy to assemble and disassemble to transport as the factory has a modular design.
- Easy to increase capacity when required by adding more molds and cutting machines
- Produce high-quality bricks with no sticky residue (unlike when using battery molds), hence easier to handle
Materials required:
For 1m3 of bricks weighing 850kg/m3, materials needed include:
- Cement PC40: 330 - 350kg
- Sand: 430-450kg
- Water: 200 liters
- Concrete foaming agent: 0.65 - 0.7kg
Clc blocks manufacturing process
Step 1: Lightweight concrete is mixed in MasterMix mixing machine (capacity 0.5m3)
Step 2: Lightweight concrete mortar is poured into molds and cast into one large blocks (size 2400x500x200mm)
Step 3: After 3 hours, use MiniCutter cutting machine to cut molds into bricks (size 100x200x500mm)
Step 4: Cure bricks by spraying water in the curing area for 3 weeks. After this time bricks can be provided to construction sites.
Equipment needed for CLC block production line
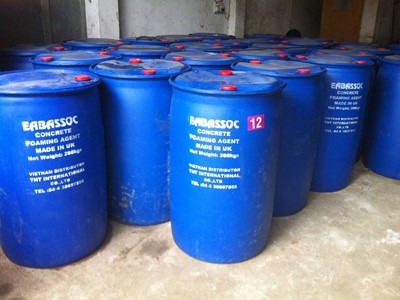
Concrete foaming agent
Our Foaming Agent is highly concentrated, highly efficient, with low dosage
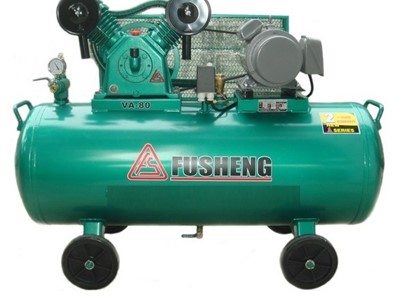
Air Compressors
Capacity 3Hp, working pressure 7kg/cm2, Volume 120 liters
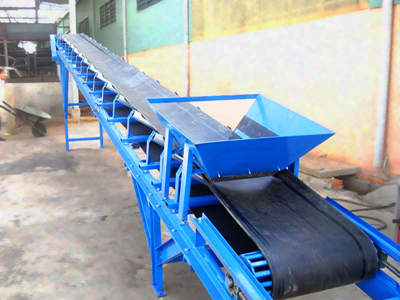
Conveyor belt
Size: 4x400m, for moving sand and cement to the mixer
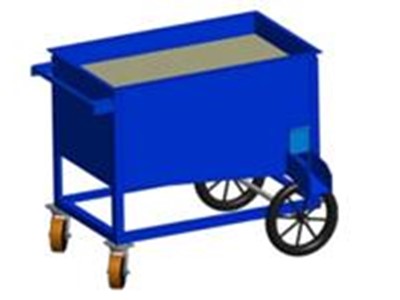
Mortar pouring cart
Capacity 0.3m3, with 2 lateral gates for easy pouring of concrete into molds
Cellular Lightweight Concrete Production Line
We can design and install CLC block manufacturing plant with the capacity from 10 to 200m3/day
Lightweight Concrete Equipments
Share your project details with us, and we'll ensure the right team member gets back to you promptly.